What is PDCA? When should PDCA be applied?
One of the principles that created a breakthrough for the Japanese economy in the 90s was “continuous improvement” with the PDCA cycle. This was considered the guiding principle in the production of enterprises at that time.
Along with the constant fluctuations and development of the economy, today PDCA is still applied effectively by businesses.
In this article, Bemo will provide an overview of PDCA – a well-known looping model that helps managers improve the value of products/services for their businesses.
1. What is PDCA cycle?
PDCA is a cycle developed and used in production and business administration through monitoring and finding defects in the process, thereby promptly changing and providing solutions to overcome errors. PDCA stands for the words Plan – Do – Check – Act to describe these jobs are always done sequentially, continuously and optimize management efficiency:
- Plan: planning, preparing resources, defining goals and scope of implementation.
- Do: implementation, implementation of the proposed plan.
- Check: check and evaluate the performance results.
- Act: based on test results, make changes, improve work.
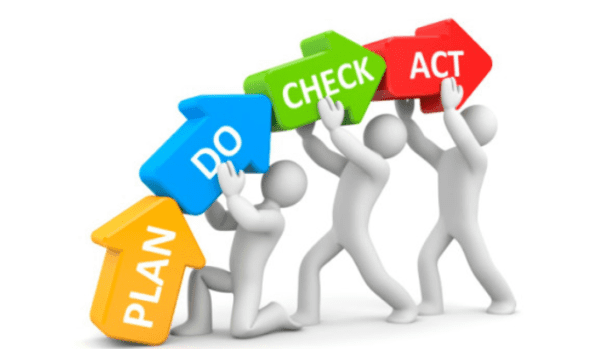
This four-step cycle should be a closed and continuous cycle that allows managers to detect and solve problems quickly and effectively and achieve goals. This is considered a scientific method that brings optimal efficiency to businesses of different sizes.
So what are the specific benefits of PDCA? Let’s find out with Bemo in the section below.
2. What benefits does PDCA bring to businesses?
PCDA has become a powerful tool for leaders because of its flexibility. When implementing this cycle, businesses will receive many benefits such as:
- Improve operational processes: the PDCA cycle provides continuous improvement, detecting and ensuring that problems are not consistent with the actual situation of the business.
- Changing the way of management and administration: PDCA not only encourages development, not afraid to change, but also is a tool to help managers adjust, change the way of governance and run the business better and more smoothly.
- Performance management, increasing competitive advantage: this loop helps administrators easily control work, capture employee activities immediately and make timely adjustments to improve and enhance work performance. Moreover, PDCA promotes synergies between different processes, thereby helping businesses speed up their business cycles and increase their competitiveness in the market.
- Quality management: easily apply ISO quality management systems such as 9001, 22000, 14001… in the operating process of the business. PDCA improves quality from planning, collecting and analyzing statistical data, thereby finding the root cause of problems in governance. This reduces the deviation of the plan from the vision of the business.
- Improve employee capacity: during the application process, PDCA not only helps businesses operate better, but this cycle can also help individuals to recognize, evaluate and make plans to improve themselves.
With the above benefits, when should businesses apply PDCA to their management process?
3. When should PDCA be applied?
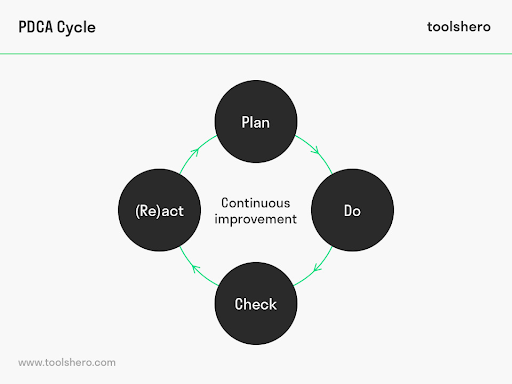
For an enterprise, PDCA is considered and applied when management levels realize problems in management such as declining sales, discrete, inefficient and wasted working processes… Now, the PDCA cycle should be applied to correct errors and improve results. Once successfully implemented, leadership can consider establishing this cycle as the norm for internal operations.
Normally, businesses should apply the PDCA cycle in the following cases:
- Launch a new project, a process in the business or improve an existing process to ensure results as planned.
- The management process encounters problems affecting employee performance, enterprise resources, and it is necessary to identify the causes of bottlenecks and errors in operation.
- Plan data collection and analysis to identify business priorities and problems.
- The management wants to optimize the management by the method of continuous improvement to increase the size of the business and standardize the working environment.
Whenever businesses want to improve and enhance the quality and value of products/services, PDCA is the model that businesses need to apply. However, implementing this cycle requires perseverance and a reasonable allocation of resources to bring the expected results. Therefore, this is not the optimal choice for businesses to solve urgent problems that need immediate results.
In addition, businesses can combine PDCA with an overall corporate governance solution to support better management. If you are looking for a software that meets the above needs, let Bemo be your business companion!